High-Temperature Molten Salt Pumps and Valves
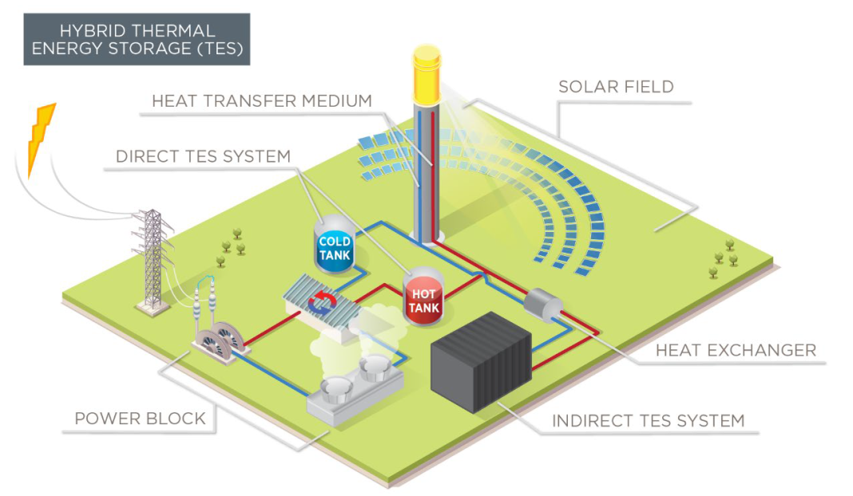
Overview
Overview
Currently, there is a major effort to operate Concentrated Solar Power (CSP) plants at peak temperatures above 700 ͦC. In this temperature range, supercritical CO2 (SCO2) cycles are slated to reach ~ 50% efficiency, which is a 25-30% increase relative to the steam Rankine cycles used in current plants. However, such a shift to higher temperatures brings with it many problems associated with materials. One of the places where material properties become critical is in the pumps, which circulate molten salt throughout the plant. In this respect, usage of existing materials such as Ni alloys in the pumps could involve operating the materials near failure, depending upon the pump design. Thus, our group is working the development and demonstration of alternative materials, namely refractory materials, that can be used for the high-temperature pumps needed in future CSP plants.
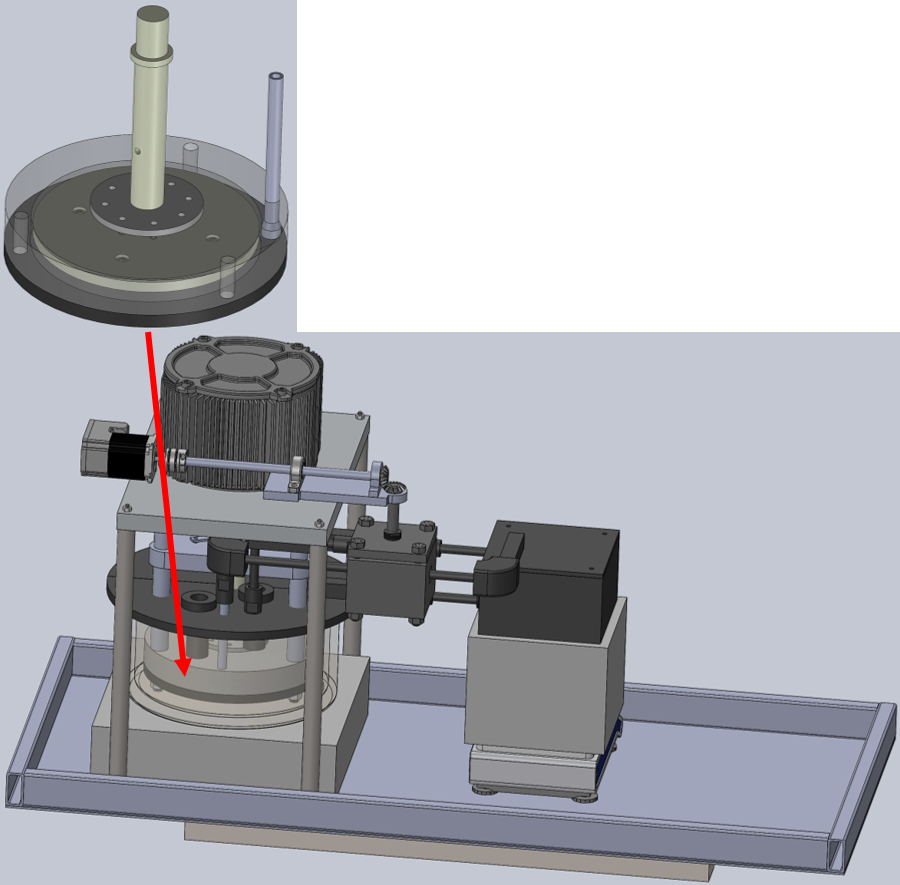
Challenges in centrifugal pump impellers
There are two major challenges for the pump impellers:
- The impeller may creep and rupture when fabricated at large diameters and run at the high speeds needed for the plant.
- The impeller may corrode rapidly in the molten salt, due to convective enhancements.
Our group is, therefore, building a test setup designed to perform the creep and corrosion tests on the impeller. The candidate refractory materials for the impeller are zirconium carbide tungsten (ZrC/W), tungsten, molybdenum and carbon fiber composite.
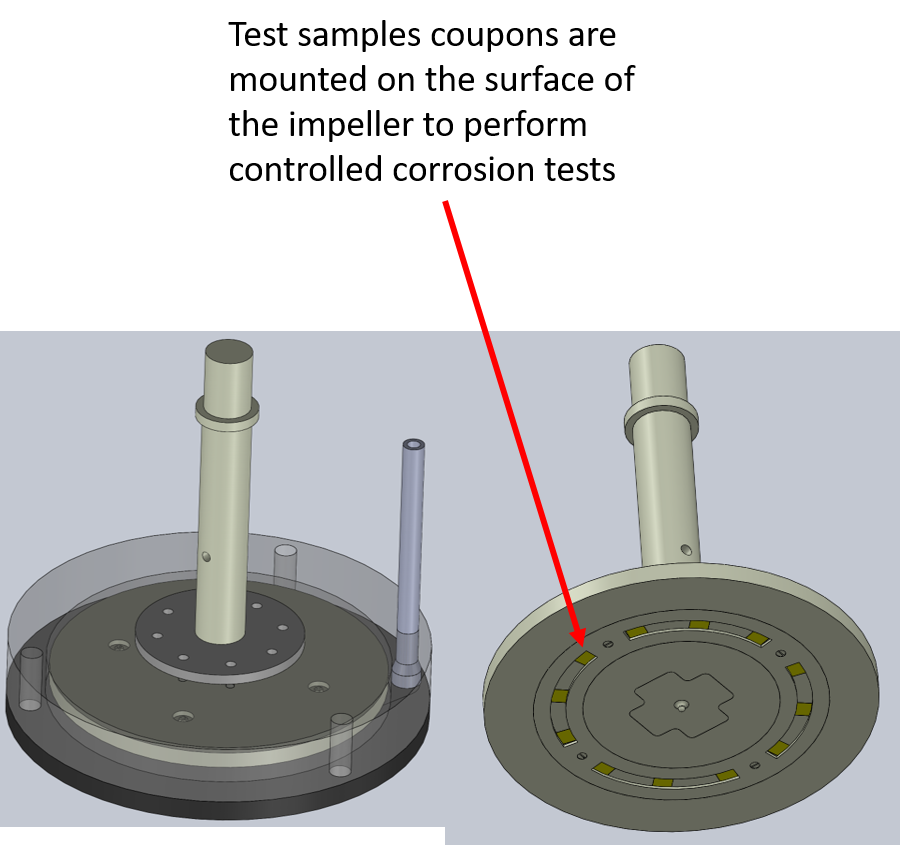
Features in our pump test
- The 8” diameter impeller will rotate at 6000 rpm. At this high speed and diameter, our lab scale impeller will experience the same level stress occurring in a full-scale impeller (22”, 3600 rpm) used in pumps for full-scale CSP plants. At the same time, the pump should only generate minimal head and about a 1 gallon per minute flow rate to fit in the small lab-scale experiments to be tested in the ASE lab facilities.
- The impeller is designed to carry multiple 1 cm X 1 cm square shape coupon samples to perform the corrosion tests. These samples will be exposed to the same high-velocity convective environment as the impeller and will provide insight into whether or not certain materials will experience enhanced corrosion when used in a pump.
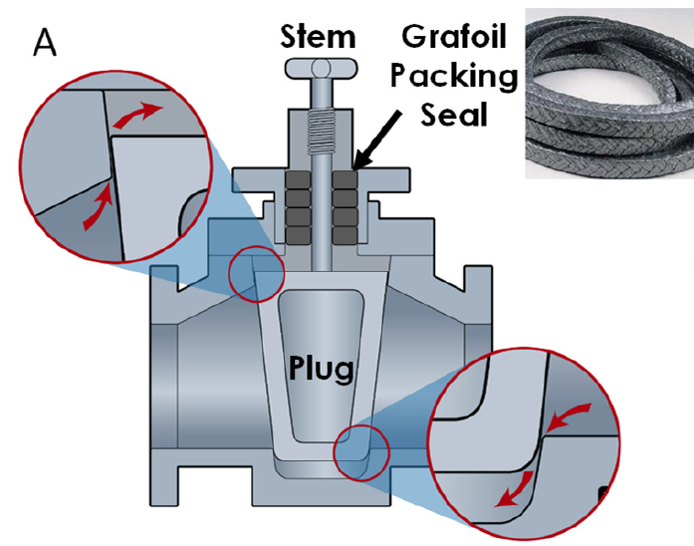
High temperature plug valve
One of the challenging aspects of making a plug valve is the tight tolerances required to minimize the leak rate. The extent to which the valve can block the flow is dictated by how tightly the plug and body are sealed against each other. A graphite plug valve has been successfully fabricated, whereby the same exact lathe settings used to cut the tapered shape of the plug, were immediately used to cut an identical shape into a steel rod that then served as the tool used to cut the mating shape into the valve body. However, because graphite erodes easily, we expect that a Molybdenum version would exhibit a longer life without performance degradation.
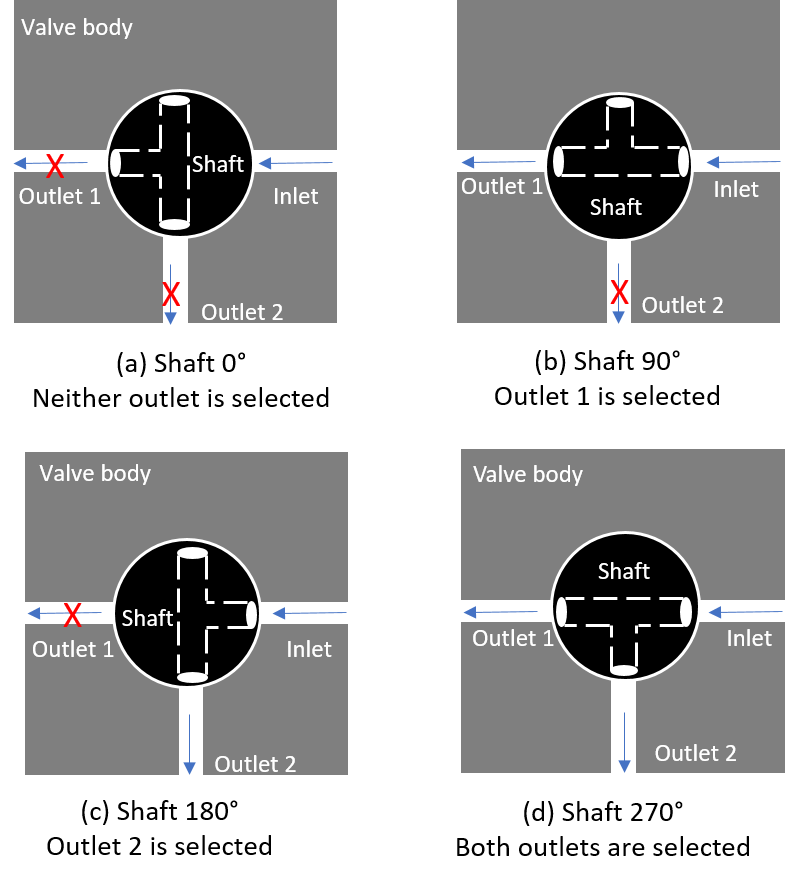
Valve working principle
A three-port plug valve is being used. The design allows testing without obstructing the flow during the molten salt circulation. The plug valve works as a selector valve by rotating the shaft a quarter-turn (90 degrees) each time.
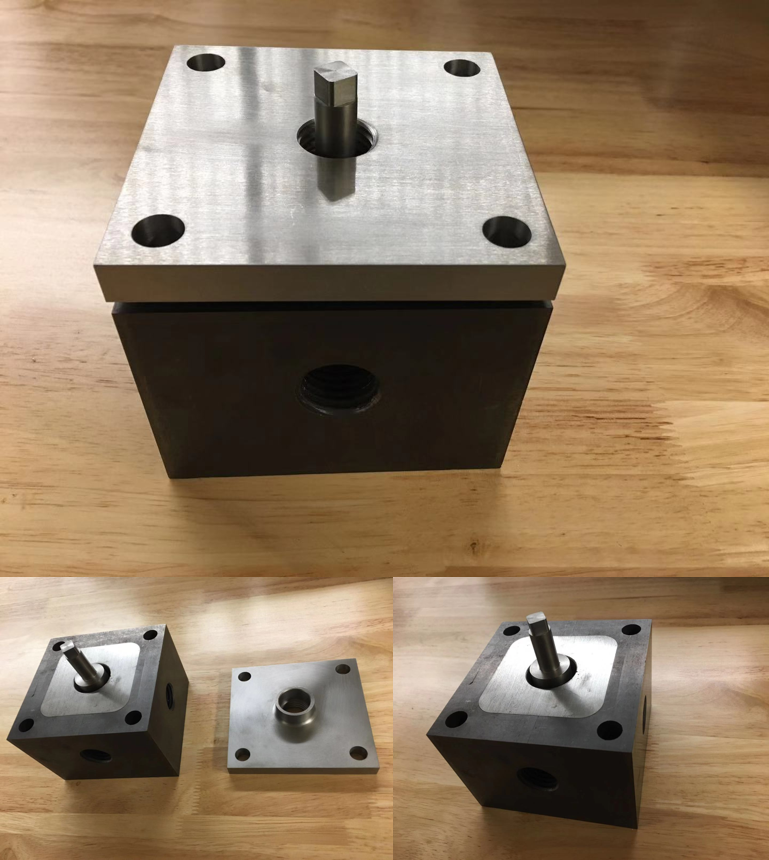
Valve components and seals
The main components are the valve body and valve shaft. They are made of Molybdenum due to its good erosion resistance and three types of grafoil seals are used in the valve to prevent leakage.
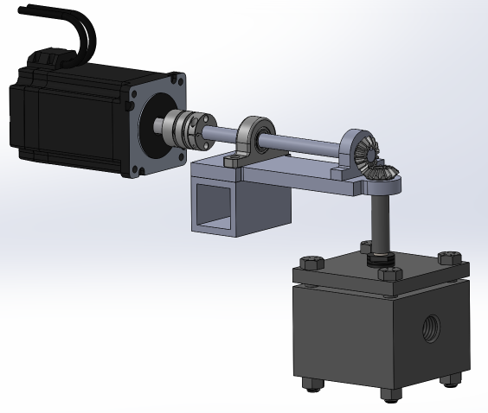
Actuation system
A motorized actuation system is used to drive the valve shaft to rotate it and control the liquid flow path. Due to height limitations in the inert chamber, the motor is positioned horizontally at 90 degrees from the shaft, with a pair of gears to transmit the torque.