High-Temperature Molten Salt Tanks and Pipes
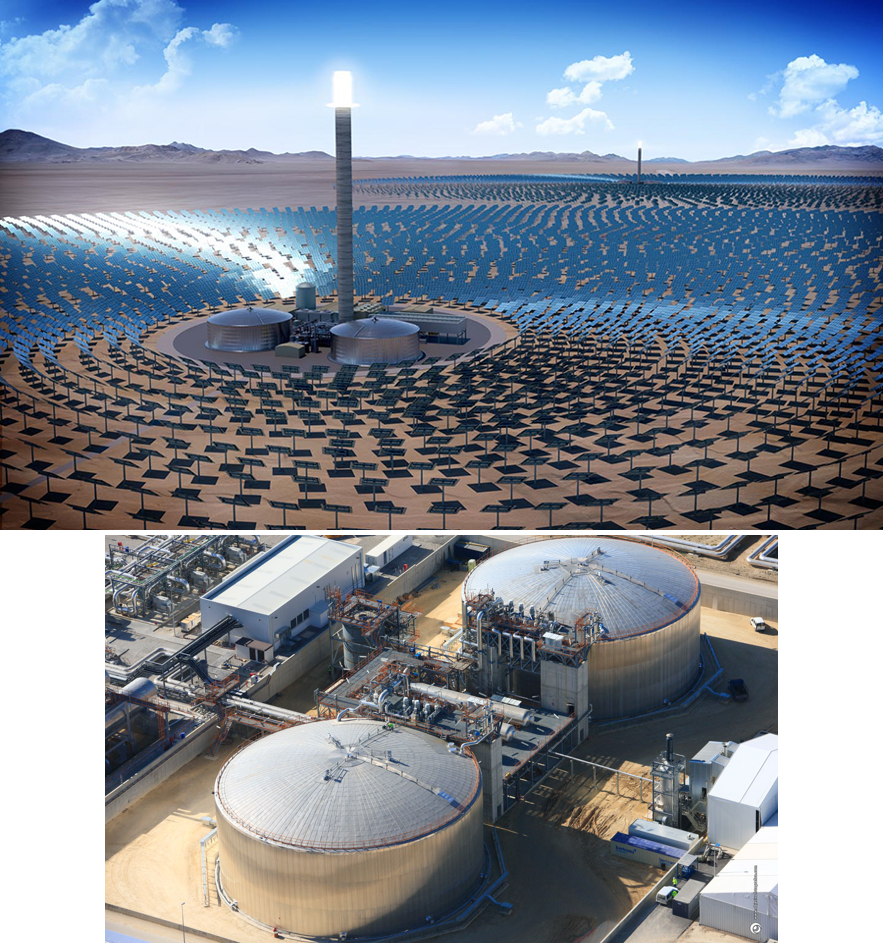
Overview
- Concentrated solar power (CSP) plants can become cheaper if they become more efficient, but this will require operating the plants at higher temperatures. However, doing so creates a myriad of new materials issues, specifically with respect to corrosion. Thus, new materials and component designs are needed in many parts of the plants to enable higher temperatures.
- One of the key challenges or high temperature CSP is then the storage tanks. It has been envisioned that a nickel alloy based piping infrastructure will work if the storage fluid is a molten chloride salt, but the nickel alloys are too expensive to use in a traditional tank design. A previously developed cost modelling framework for thermal energy storage (TES) tanks estimated that if nickel (Ni) alloys were to be used in the CSP infrastructure, such components would be at least 4X as expensive. [Amy et. al., Nature volume 550, pages 199–203, 2017]
- In this project, we are demonstrating a new approach, where ceramic castable cements can be utilized as a cheaper alternative to nickel alloys for both the tanks and piping system.
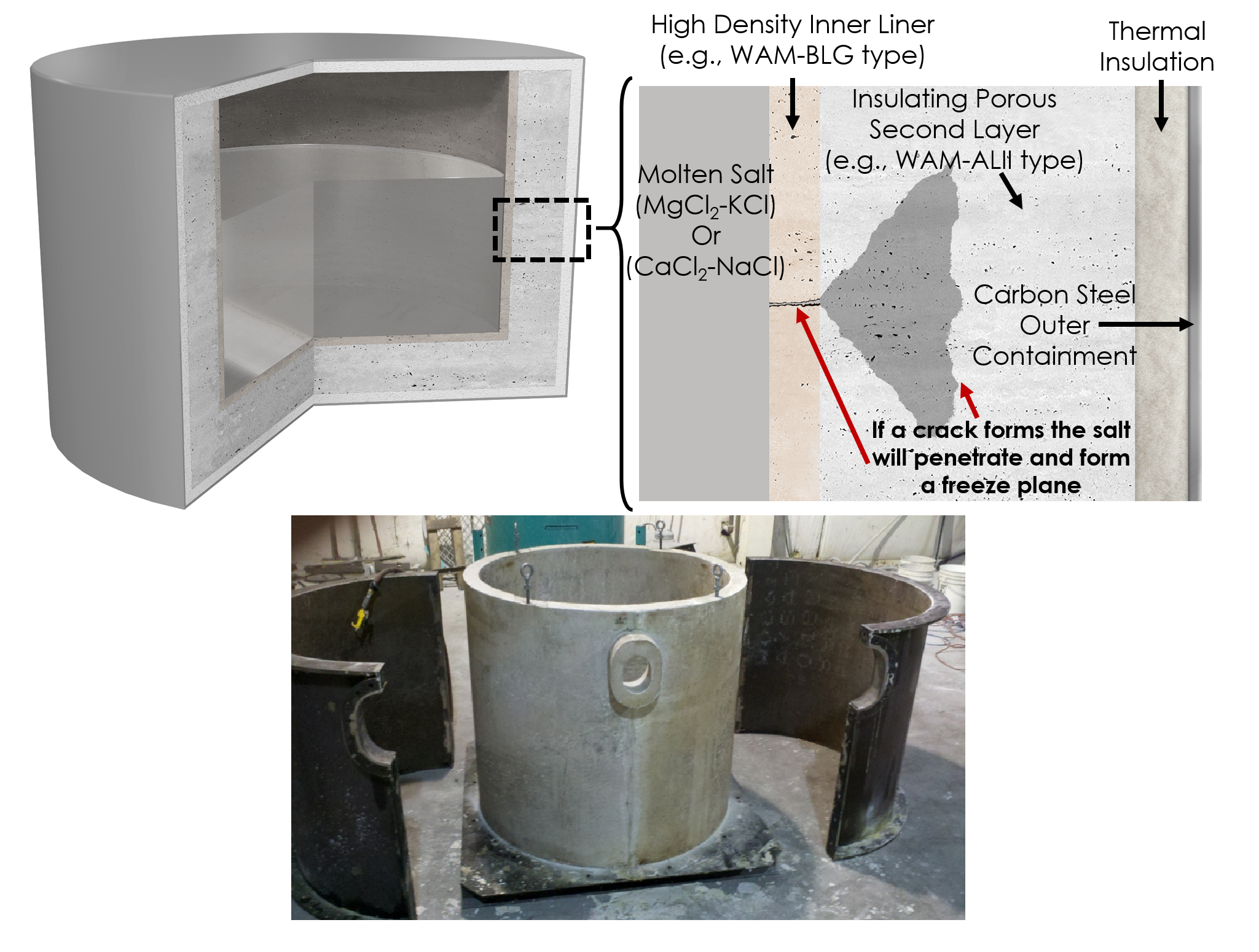
What is castable cement?
- What is castable cement?
Castable cement is like a high temperature concrete. It starts as an inexpensive powder, that can be purchased in 100 lb bags from our collaborators Westmoreland Advanced Materials [https://westadmat.com/]. The powder can be mixed with water to form a slurry that can then be cast into any desired shape using a mold, just like regular construction cement/concrete. The cement then undergoes several curing and heat treatment steps at temperatures below 700C, yielding a final part that retains the molded shape. The resulting material is then a ceramic, whose composition and microstructure can have been engineered for different applications, such as compatibility with molten salts, or liquid metals such as aluminum (see example video [https://westadmat.com/aliimovie/]
- What is our approach?
We plan to use a series of castable cement materials including a denser cement that is used as a primary liner (~ 10 cm), and a much thicker (~ 1 m) secondary more porous liner is used as thermal insulation and as a backup container that can form a freeze lining. This secondary layer will have lower thermal conductivity and will therefore act as insulation and also as a secondary protection against leaks.
- Advantages of multi-lined castable cement
The proposed design includes a three leak protection mechanisms. First, the inner most layer should be impenetrable. Second the thicker insulating layer will be designed to prevent penetration into its pores, via volume filling reactions. Third, the secondary layer is made sufficiently thick that it will form a freeze lining (i.e., any leaking/penetrating salt’s temperature will decrease to its freezing point and plug itself, preventing further spread of the leak).
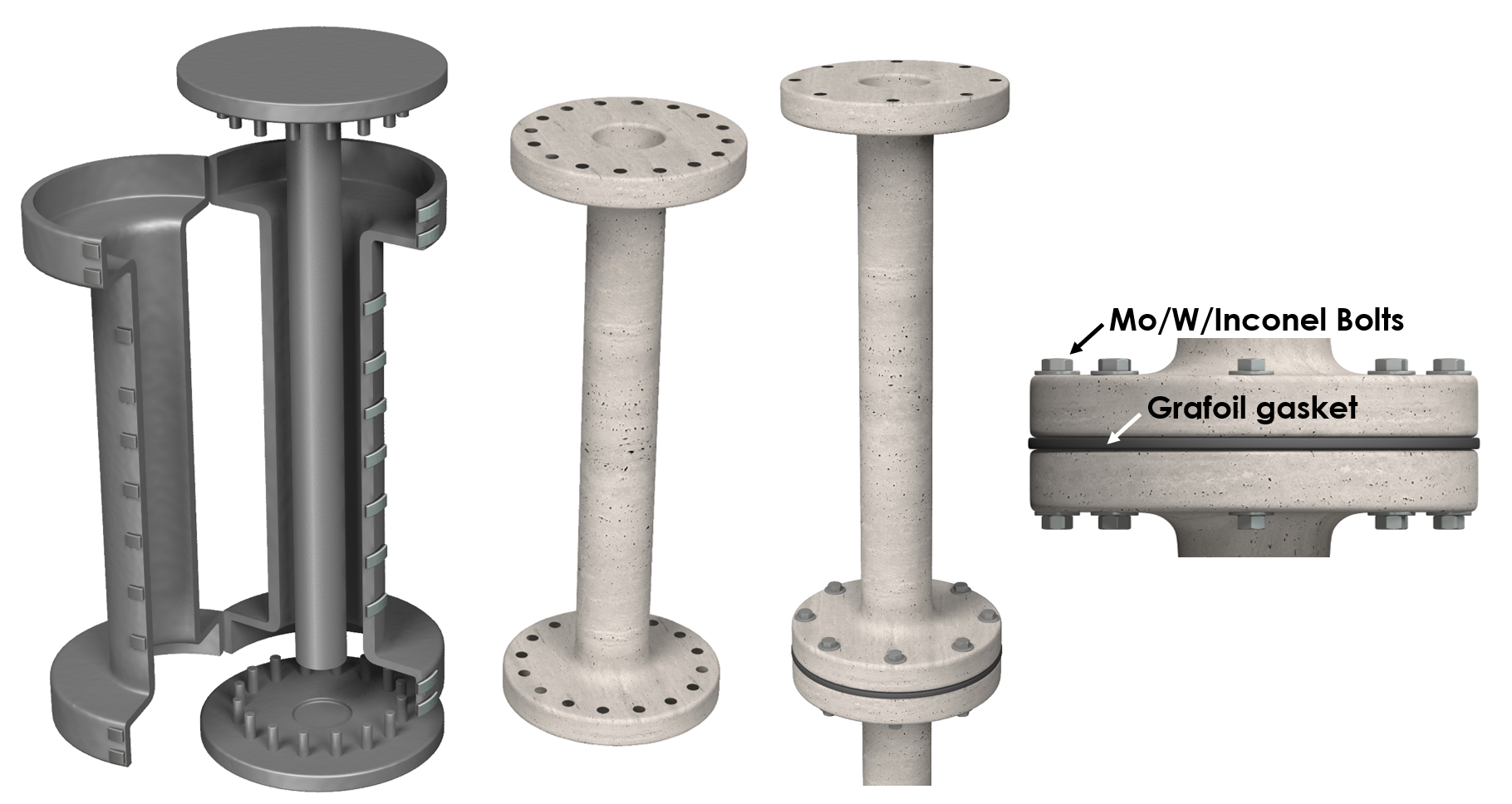
Castable cement, more to offer?
One major advantage of castable cement is its ease of fabrication, whereby one simply adds water to the powder to form an emulsion, just like construction concrete/cement. This emulsion is then poured/injected into a mold to set the final shape.
Since castable cement offers an inexpensive route to a refractory and chemically compatible material for high temperature molten salts, we are also expecting additional cost savings by employing castable cement to make piping network for transporting salt between different subsystems and up/down the power tower.
In this project, our goal is to demonstrate that castable cements can be used to make flanged pipe sections. This will offer a lower cost alternative to nickel alloys such as Haynes 230, to form a corrosion resistant infrastructure for handling high temperature molten salts.
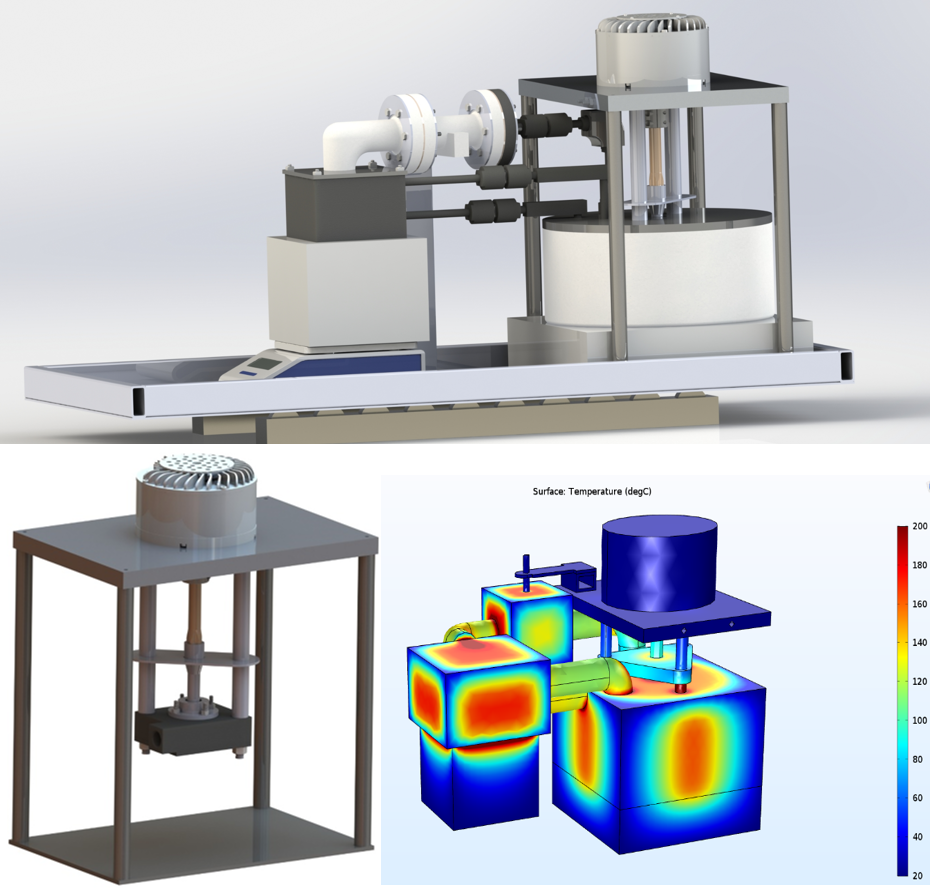
Setup design and analysis
- To deploy this new concept, we are building a continuous circulation loop that has a castable cement tank, a graphite pump, piping network, a flow meter and also a castable cement flanged pipe section. The purpose of this loop is to test/prove two things:
- (1) We plan to show that the castable cement resists corrosion and penetration by the molten salt, even when subjected to convective effects driven by the pumped circulation loop.
- (2) We plan to show that the castable cement can be made into a functioning flanged pipe section without leakage (the white components in the Fig. are cement parts, while graphite components are shown in black).
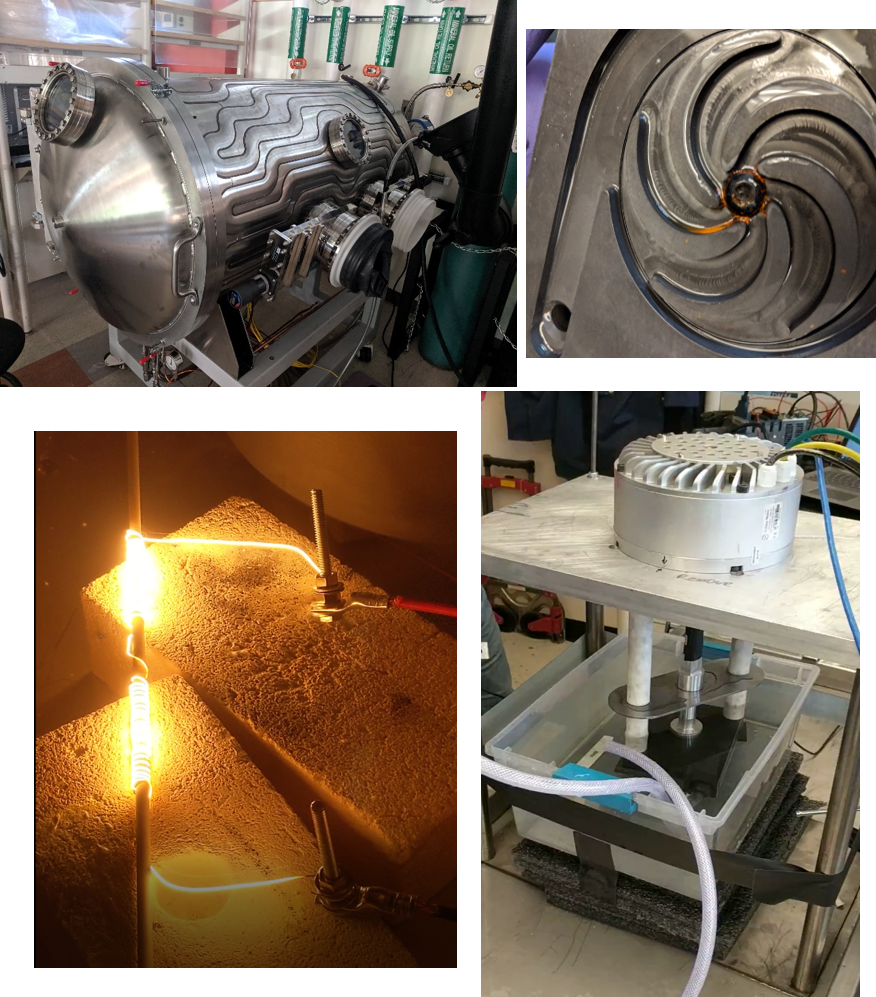
Molten salt setup construction
- The whole setup together with its components will be placed inside a vacuum chamber and held in a 1 atm inert environment.
- A centrifugal submersible/sump pump made of graphite is designed to circulate the molten salt through the entire salt loop.
- The heaters in this setup are custom heaters made of tungsten wire due to its high melting point. The 2” long glowing tungsten coil provides up to 1 kW power at 1500°C.