Printed-Circuit Heat Exchanger (PCHE)
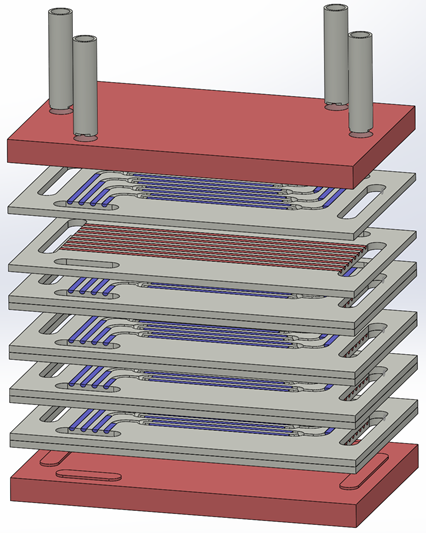
Overview
By operating concentrated solar power (CSP) plants at higher temperatures than current designs (i.e., > 565 °C), the plant efficiency can be increased, which can then reduce the levelized cost of electricity (LCOE). Next generation CSP plants envision the usage of a new type of turbine system that operates at both high temperature and high pressure. Current targets from the department of energy are to develop CSP plants with peak operating temperatures above 750°C and as a result, one of the key components that is being developed for next generation CSP plants is the primary heat exchanger. The heat exchanger transfers heat from whatever medium is used to store the sun’s energy (e.g., a molten salt), to a compressible fluid such as a gas or supercritical fluid such as supercritical CO2 (SCO2). At the temperature and pressure of interest new materials with higher strength than steel must be used.
Given the high pressures and high temperature, it can be advantageous from a cost perspective to use a heat exchanger that has small channels so that the total force applied by the high pressure fluid e.g., supercritical CO2 (sCO2), on the walls of the channels is small (note that the force is equal to the applied high pressure times the small channel’s surface area). With the total force being small, it enables usage of a minimal amount of material i.e., on the order of millimeters thick to withstand the high pressure, thus reducing the total amount of material needed in the heat exchanger and making the entire heat exchanger easier to manufacture.
Towards this end, printed-circuit heat exchangers (PCHEs) are envisioned to be used to transfer thermal energy from primary molten salt to sCO2 in next generation CSP plants. A PCHE contains many small millimeter scale channels often machined or chemically etched into individual plates, which are then stacked together (see Fig).
Currently, PCHEs capable of effective heat transfer from molten salt to sCO2 at temperatures > 700 °C are not commercially available, owing to critical limitations of metal alloys. Current PCHEs made of stainless steel, with a temperature limit of ~550 °C, cost in excess of $0.1/W, while typical heat exchangers usually cost less than $0.05/W. Use of higher-strength, high-temperature Ni-based superalloys would lead to a major increase in cost that could negate the cost reduction associated with using a higher temperature turbine in the first place. Thus, low cost PCHEs that can operate in high-pressure sCO2 at >750 °C remain to be developed and is one focus of our work.
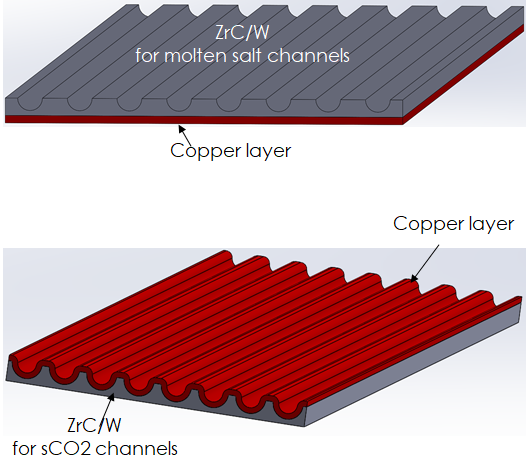
Objectives
We aim to lower the cost, advance the performance, and reliability of PCHEs based on a robust ceramic/refractory metal composite (i.e., cermet). The patented cermet is made of zirconium carbide and tungsten (ZrC/W) by our collaborators at Purdue University, led by Professor Ken Sandhage. ZrC/W cermets possess an unusual and very attractive combination of high-temperature properties for use as PCHEs, and the material can be fabricated via a novel low-cost forming and net-shape/size reactive conversion process. Both ZrC and W are very hard materials to form on their own. However, the novel process invented and developed in Professor Sandhage’s group overcomes this by first forming another material that is easy and cheap to form, into the desired final shape. Once formed the part is then exposed to a liquid metal that causes a chemical reaction to occur, and amazingly the original shape is preserved. During the reaction, the starting material is converted to ZrC/W and in this clever way, hard to form, high strength materials can be cheaply made into complicated shapes such as the plates needed for a PCHE.
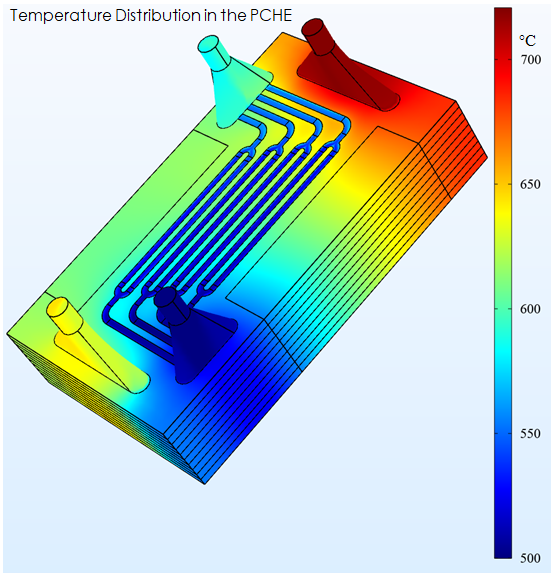
Challenges in PCHE Design
1) Most current thermal-hydraulics design of PCHEs use one (or several) channels as the analysis domain, and assume that periodic pattern applies for the whole PCHE. The header region, which is the portion that distributes the flow into the channels from a pipe inlet, and the plate region are often studied separately. This approach has its necessity since it is usually impractical to simulate the entire heat exchanger, due to computational expense (i.e., it will take a long time for a computer to finish the calculation). However, in reality the flow in header region and plate region strongly interact with each other. Idealized conditions assigned to header region or plate region may not reflect the true behavior/performance of the PCHE.
2) Most of the existing PCHE studies have focused on the thermal-hydraulics side of the problem, i.e., pressure drop, heat transfer, thermal capacity, etc. However, one of the biggest challenges with PCHEs is on the thermo-mechanical side, e.g., stress, creep, fatigue of the PCHE material and joints. Most often, the thermal mechanical performance eventually determines the safety, reliability, and economics of the PCHE.
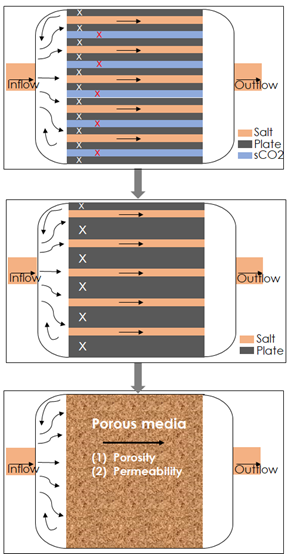
Thermal-Hydraulics Analysis
A more accurate way to analyze the PCHE, especially the header region, is to analyze the PCHE as a whole domain. In order to overcome the issue of an exceedingly large computational cost, we have taken the approach of representing the stack of plates as a porous media. The porosity of the porous media depends on the geometrical dimensions of the PCHE, and the permeability of the porous media is chosen to that the porous media generates the same pressure drop as the stack of plates. By simulating the whole PCHE domain, we are using a more realistic boundary conditions for the header analysis, than assuming constant outlet pressure at the header. Results from simulations of the entire domain using a porous medium appaorch will provide a better assessment of the maldistribution of flow through the channels for a specific header design, and will allow us to optimize the header design for better PCHE performance.
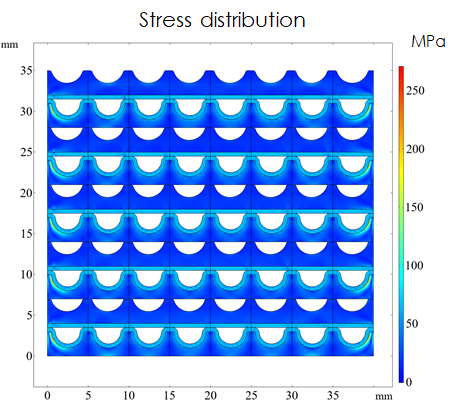
Thermal-Mechanical Analysis
Our research involves designing PCHEs so that the imposed stress due to thermal and mechanical effects is well below the failure strength of component materials and joints. Of particular concern is the stress generated due to the coefficient of thermal expansion (CTE) mismatch between PCHE plates and bonded foils used as corrosion protective layers/coatings. We’re also investigating the effect of compressive stresses, via the use of external clamps, to compensate for the elevated pressure within the sCO2 channels. This approach can increase the reliability of the joints by increasing their failure stress. The thermal-mechanical analysis will help take maximum advantage of the high stiffness of ZrC/W at high temperatures, yet manage the induced stress due to thermal, mechanical, and CTE mismatch effects.