CO2 Free Hydrogen Production
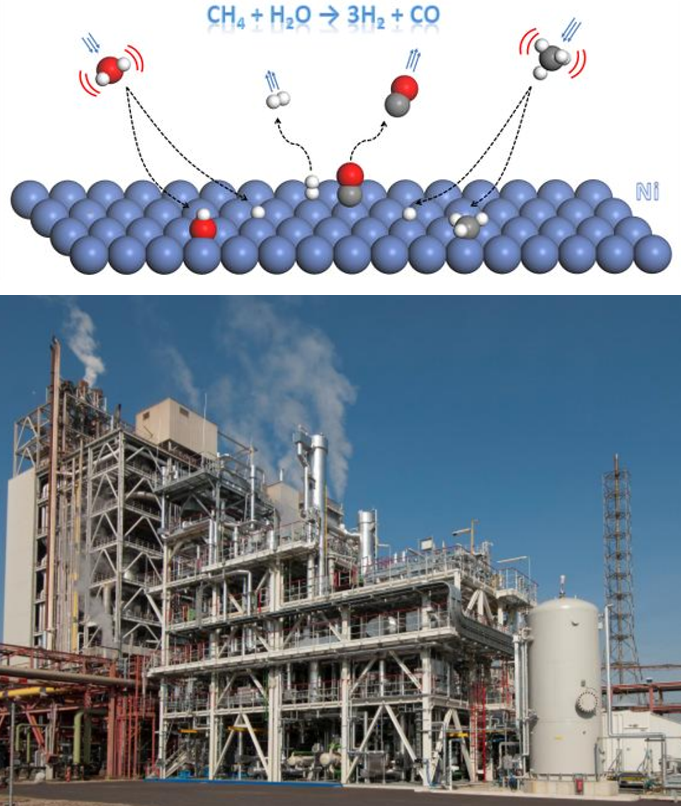
Currently, the predominant way we make hydrogen is by reacting methane (natural gas) with water, via steam-methane reforming and the water gas shift reaction (SMR+WGS). The problem is that this process relies on the formation of CO2, and globally it is responsible for about 1% of CO2 emissions. Thus there is a need to develop a new approach to making hydrogen that is CO2 free.
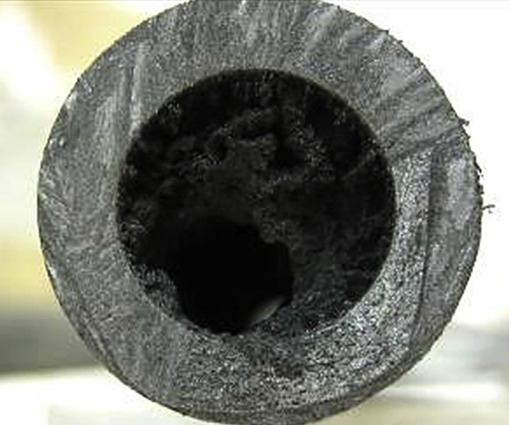
One alternative approach to SMR+WGS is to instead directly pyrolize methane. If one were to heat methane (CH4) up to ~ 1400°C, in a inert environment without oxygen, instead of burning it will decompose into solid carbon and gaseous hydrogen. The simplest way this can be done would be to heat the CH4 in a tube. But the problem is that when the pyrolysis decomposition reaction occurs the solid carbon will deposit on the walls of the tube, and very quickly it will build up and block the cross-section (see figure). As a result the solid carbon will plug and clog the reactor, which would prevent continuous operation, which is needed for it to work economically/practically. However, Prof. Thomas Wetzel from KIT has come up with a clever way to get around this problem, which is to use an inert liquid such as tin to carry out the reaction and prevent clogging.

We are continuing to develop Prof. Wetzel’s idea by utilizing the hardware we developed that enables us to pump liquid metals, such as tin, at extremely high temperatures with long life. Here we’re developing a bubble column reactor, that uses liquid tin at 1400°C to facilitate complete pyrolysis of CH4. Currently this work is unfunded, but the effort is ongoing to find support. The idea is that CH4 is bubbled up from the bottom of the reactor. Inside each bubble, the reaction occurs while it rises through the tin. By the time it reaches the surface the entire bubble has reacted and the bubble contains solid carbon particles that will float on the surface because of the large density difference between carbon and tin. The hydrogen then exits the reactor from the top, and the tin can be pumped to continually remove the carbon. As the carbon exits, it is cooled in a heat exchanger before it is separated from tin by a cyclone. A special type of liquid droplet heat exchanger is also used to recuperate the sensible heat in the hydrogen stream. In this way the entire system can be very efficient and cost effective.